電池不要のセンサーでIoTの世界に挑む。泰興物産が見据える新たな地平
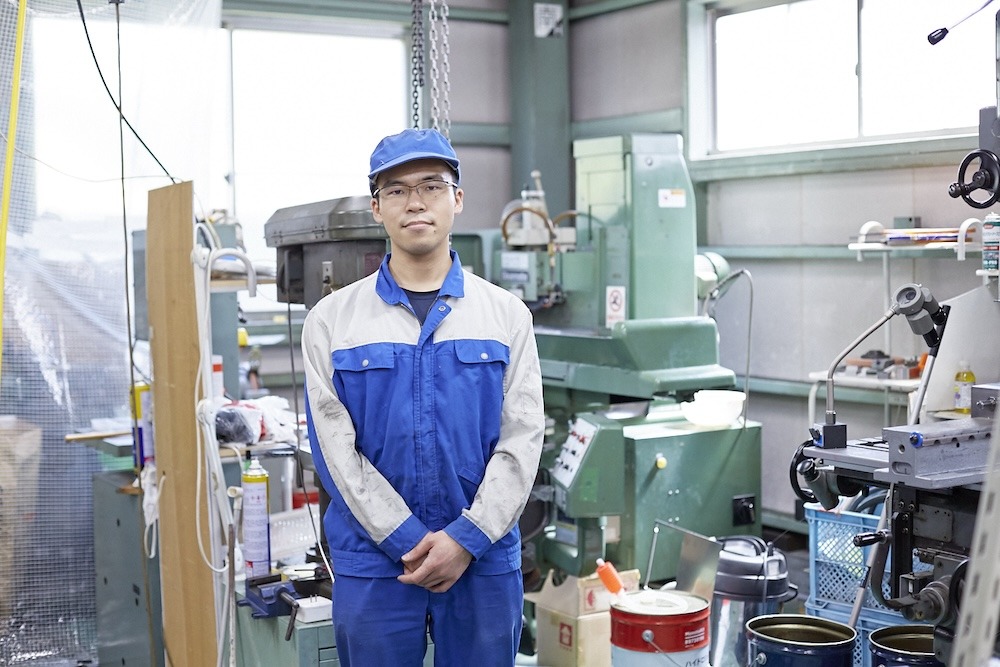
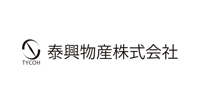
社名 | 泰興物産株式会社 |
業種 | 製造業 |
利用サービス | BizStack |
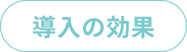
💡IoTビジネス開発 💡データ可視化 💡遠隔監視 💡ベンチャー共創 💡業務効率化 💡センサーメーカー
AIの興盛とともに脚光を浴び続けるIoT。AIの進化に欠かせない技術を支えるのは、様々な機器に取り付けられるセンサーです。
2023年「IoTの社会実装を進める上で必要不可欠なセンサーの開発を促進すること」を目的に、MODE, Inc.(以下、MODE)が主催する「MODE Sensor Award」(以下、Sensor Award)が開催されました。見事にMONOist賞に選ばれたのは東京都日野市に拠点を置く泰興物産株式会社(以下、泰興物産)です。
泰興物産が開発したのは、電池が不要な「C3-less電力センサ」。今回はその開発ストーリーと展望を、同社製造部の丸田 哲郎氏に伺いました。
泰興物産が有する「中品種中量生産」という強み
―泰興物産の主要な事業内容について教えてください。
当社は射出成形技術をコアにプラスチック製品の生産を手がけてきました。創業当初は化粧品の容器から事業をスタートしており、口紅の繰り出し容器などがその典型です。
現在では化粧品業界に留まらず、自動車業界など様々な業界の企業とお取引しています。特に近年は、医療機器や半導体業界から多くの依頼を受けて、医療の検査器具や電流が流れるコネクタのような部品を生産しています。
―創業はいつですか。
1975年です。今年でちょうど50期を迎えます。当時この一帯は工業地帯で、多くの工場が存在していましたが、現在では宅地化が進んでいます。しかし、私たちのように当時から変わらず操業している町工場も存在するのですよ。
―50期続いてきた泰興物産の強みはどこにあるのでしょうか。
私たちがお客様に選ばれている理由は、「中品種中量生産」に対応できる柔軟性にあると捉えています。
射出成形でプラスチック製品を製造する企業は、できるだけ大きなロットを受注する傾向にあります。その方が射出成形の特性も活かしやすく、利益も出しやすいからです。材料についても、特定のものにだけ対応する企業もあるほどです。
一方当社では、小ロットから中ロットまで対応可能で、かつ材料にもこだわらず対応できます。そこがお客様からご評価いただいている点かと思います。
―なぜ柔軟な対応が可能なのでしょうか?
ベースとなる当社の技術力の高さもあるかと思います。私の祖父が立ち上げた当社ですが、父は特級プラスチック成形技能士の有資格者をはじめ多数の技術的な資格を保持しています。母も高専を卒業しており、工場のライン管理を緻密に行えます。平均年齢23歳の小規模な組織ですが、高専卒の優秀な若手技術者も在籍しており、およそ50社のお取引企業様からの依頼にできる限り応えるなど、日々チャレンジしていますね。
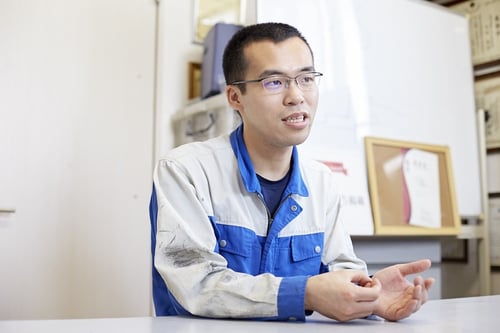
C3-less電力センサが顧客から支持される理由
―Sensor AwardでMONOist賞を受賞したC3-less電力センサについて、どのような特徴があるのか教えてください。
最大の特徴は、「電線に流れている電流を電池なしで計測できること」です。これにより、電池交換の手間が不要となり、特に大量のセンサーを使用している工場などでの管理の負担が大幅に軽減されます。
また販売価格も従来製品の半分ほどに抑えることに成功しています。これもお客様からご好評をいただいている要因ではないでしょうか。
―電池が不要になるメリットについて、詳しく教えてください。
例えば3,000個のセンサーがある場合、1年間に1回電池が切れると、年間で約3,000個の電池交換が必要となりますよね。一日に換算すると約100個以上、電池の交換作業が発生するわけです。C3-less電力センサを活用すると、単純にその手間が省けます。
また電池が不要になることで、センサーをより小さくできるというメリットも生まれます。例えば単三電池が必要になると、その分センサーが大きくなってしまいますので、設置できる場所が限られてしまいます。
―C3-less電力センサは実際にどのような場所に設置されていますか?
主に工場で設置されています。設備の稼働状態をリアルタイムで監視し、異常があればすぐに対応できるようにするためです。C3-less電力センサは大きな設備だけでなく、その内部のヒーターやポンプといった部品単位にも取り付けが可能です。これはダウンサイジングしているC3-less電力センサならではの強みが発揮されているといえるでしょう。
また、古い生産設備に後付けすることも可能です。従来のセンサーは古い設備に設置する場合、配電を再検討したり、それを行うために資格を持った技術者が必要だったりしたわけですが、C3-less電力センサはそのような作業は不要で、すぐに取り付けて稼働させられます。このように、あらゆるシーンで活用できるのが当社のセンサーの特徴になっています。
―導入実績はいかがでしょうか。実際に、どのような業界で使われているか教えてください。
例えば大手プラント企業様で100個ほど納入いただいています。自動車用半導体工場様の事例では、信頼性をより高めた改良型のC3-less電力センサが60個ほど活用されています。
他社との協業も生まれています。例えば、展示会にC3-less電力センサを展示していると「このケースはどこで作っているのか?」と聞かれることがあります。その際に当社で生産していることをお伝えすると、ケースの注文をいただくこともありました。
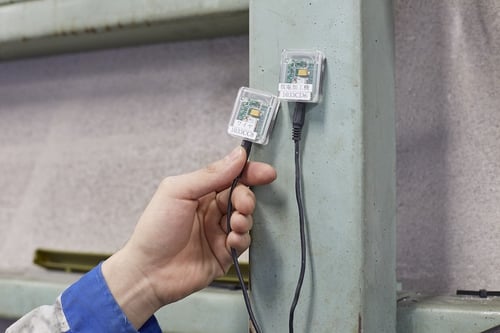
タッグを組んで実感した高専と共同開発するメリット
―センサーの開発はいつから始まったのでしょうか。
2018年頃だったと記憶しております。当初は私の母校でもある東京工業高専にある、水戸研究室で研究開発がスタートしました。3年ほど研究を重ねて、さらに製品化に向けた開発を1年ほど行いました。
―高専と協業するメリットはなんでしょうか。
やはり「距離が近いこと」ですね。東京高専の場合、私の母校だったというのもありますが、研究室の扉を開けるとフランクに接してくださるというか。共同でお話が進めやすかったですね。
―水戸先生とは学生時代からお知り合いだったのでしょうか。
いえ、違います。私は当時別の専攻だったので、おそらく水戸先生とは廊下ですれ違ったことがあるかどうかくらいだと思います。
―そうすると、どのような経緯で共同研究を行うようになったのか気になります。
水戸研究室では、もともとセンサーの研究を行っていました。高専は近年社会実装を意識した研究を行うよう要請されていますが、その流れで高齢者の見守りを目的にセンサーを開発していました。
見守りというとカメラで行うイメージがあるかもしれませんが、プライバシーの観点からやりづらさもあります。そこで、例えばエアコンなどにセンサーをつけて、その稼働状況から高齢者の方の状況が把握できないかと考えたわけです。夏場にエアコンの電源がつかなかったら何かあったのかもしれないと気づけるわけですね。
このような背景でセンサーの開発を進め、センサーで用いられる電子基板は完成しました。しかし、それを保護するケースの開発に難航してしまいます。当初は3Dプリンターを活用していたようですが、出力する際に用いるサポート材の消費や出力後の剥がす作業がネックになっていたため、大量生産の見通しが立っていませんでした。
そこで射出成形を用いるのが良いのではないかとなり、高専の別の先生を通じて当社が関わるようになりました。当社は射出成形だけでなく、そこで用いる金型も作れますから、一緒にやりやすかったのではないかと思います。現在は特許を持つまでになり、一定の成果は出せたのではないでしょうか。
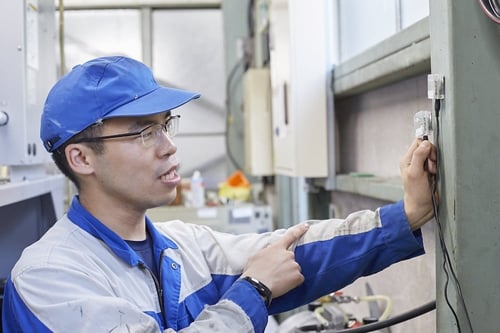
Sensor Awardは「開発者同士の交流」が最大の魅力
―Sensor Awardに参加された感想を教えてください。
まず自分の知らなかったセンサーがたくさんあることに驚きました。センサーと言っても、その多様性と適用範囲の広さに改めて気づかされましたね。
特に、同じ機能を持つセンサーでも、異なる製造技術や応用技術が存在することが多く、それぞれが特定の業界に特化している点が興味深かったです。センサーというと、基礎部品自体は1個100円くらいなのですが、用途に応じて様々な改造を施す必要があります。加速度センサーひとつとっても、様々な種類があるのはこのためです。
―Sensor Awardに参加して感じたメリットはなんでしょうか?
やはりセンサーを開発する技術者同士の交流ですね。普段なかなかできない経験でしたし、皆さん何かしら技術的な課題を抱えて苦労しているため、その苦労話で盛り上がりました。
個人的にはリコー様が開発した色素増感太陽電池のお話に感銘を受けました。私はもともと化学系の研究をしていたので、材料を固形にして電気を通すのがいかに大変か身にしみて理解しています。それだけに、これを開発する裏でどれほどの苦労があったのだろうかと考えてしまいますね。

「脱成形機」を掲げ、IoTという荒野を歩み続ける
―泰興物産の展望について教えて下さい。これからはIoTビジネスへの展開をより進めていくのでしょうか。
射出成形だけの事業では、市場の成長性が限られています。市場規模が拡大しないと、成形機を何台も並べて生産するのも難しくなりますし、収益性も落ちてしまいます。実際に撤退している企業も多く見られます。
だからこそ「脱ハードウェア」を掲げて、成形機に頼らない事業を育てる必要があると考えています。その1つがIoTですね。
―ちなみに、IoTに強い関心をお持ちになったのはなぜですか。
私は高専を卒業後にこの会社に入社していますが、高専時代はそれこそ様々な資格をとったり、プログラミングなど専門領域以外のことを学んだりもしました。
その1つで国際的な産業政策を調べる課題があり、そこでIoTの面白さに気づきました。IoT自体は1980年代から様々な試みが行われてきましたが、近年の第4次産業革命によって再び注目を集めるようになりました。IoTから得られるデータがAIの学習に用いられるため、重要なテクノロジーの1つとして各国で取り組みが進められるようになったからです。実際にドイツのIndustry4.0や日本のSociety5.0でもIoTの重要性はうたわれています。
一方でIoTを実装する上で課題があることにも気づきました。その1つがセンサーの「電源」の問題です。当時はACアダプターが主流でしたが、仮にセンサーを1,000個使用する場合、1,000個のACアダプターをつなげるのは現実的ではありません。これはいずれ解決すべき課題になるだろうと当時から考えていました。
―それが、電池不要のC3-less電力センサ開発から、現在のIoTビジネスにつながるのですね。
いえ、直接つながったわけではないのです。色々なことにチャレンジしていたら、結果としてIoTに行き着いた感じですね。
―お客様の課題に向き合うチャレンジが実ったということですね。最後に今後の展望を教えてください。
C3-less電力センサは良さもある一方で、まだまだお客さまの環境にうまくフィットしないケースもあります。そこに合わせて改善していくというのが1つの方向性です。
一方で、形状などを変えて適用させていくのもアリかなとも考えています。例えばC3-less電力センサを電源にして、他のセンサーを動かすということも可能です。
現時点では色々な方針が考えられるので、今後は時代の流れやお客様のニーズを見極めながら開発を進めていきたいですね。
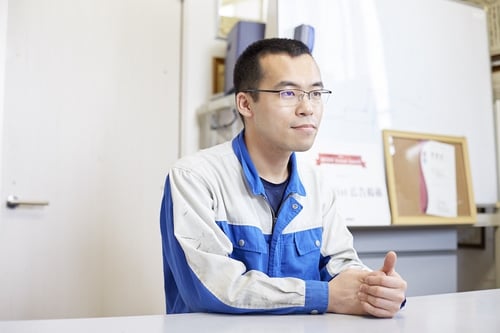